Pyrolysis
The PreZero Pyral’s pyrolysis plant is an environmentally friendly and resource-efficient thermal plant located in Freiberg (Germany).
Organic contaminants (plastics, paint, etc.) are separated from the inorganic materials (metals) at approx. 550°C without oxygen supply and independent of energy.
What does pyrolysis mean at PreZero Pyral?
An environmentally friendly and resource-efficient pyrolysis plant is operated at the Freiberg/Saxony site. It is a unique, synergetic and integrated concept, which includes the following areas:
- Thermal utilisation of the organic admixtures to the metals
- eneration of electricity from self-generated heat via steam
- Production of aluminium alloys in the aluminium smelter in various shapes and alloys
The high quality of PreZero Pyral’s products is ensured by efficient quality management. Input materials for the pyrolysis plant are waste materials containing aluminium (cans, tins, tubes, packaging, etc.). Organic impurities and admixtures support the pyrolysis process and are thus desired.
On the one hand, the resulting heat is used to heat the pyrolysis drum, thereby providing the heat for oxidation of the carbon that is still attached to the aluminium.
Pyrolysis in detail
Pyrolysis is a thermal process in which the decomposition of organic substances takes place in the absence of air at a higher temperature and the organic fraction is completely degassed.
The aim is to recover valuable materials (high-quality aluminium scrap) and to make the materials (carbon and aluminium) as completely inert as possible. The pyrolysis process is carried out in a rotary drum heated with flue gas and equipped with an inlet and outlet device. The pyrolysis process is carried out at temperatures of 550-600°C. The gas produced during pyrolysis is extracted at the end of the drum and enters a combustion chamber. In this combustion chamber, the large-molecule chain and ring compounds and the permanent gases are burned off at temperatures of approx. 1200°C.
On the one hand, the resulting heat is used to heat the pyrolysis drum, thereby providing the heat for oxidation of the carbon that is still attached to the aluminium. Secondly, the residual heat is used to heat the waste heat boiler and generate electricity via a generator. This creates an energy cycle that makes PreZero Pyral independent of electricity suppliers.
Pyradec®
The PreZero Pyral’s pyrolysis plant is an environmentally friendly and resource-efficient thermal plant located in Freiberg (Germany).
Organic contaminants (plastics, paint, etc.) are separated from the inorganic materials (metals) at approx. 550°C without oxygen supply and independent of energy.
Why is Pyradec® the solution for modern waste management?
9 reasons why Pyradec® is a solution for the future:
- 100% recycling of municipal and commercial waste
- Recovery of metals with organic attachments of up to 70%
- High, continuous throughput of 3-15 tons/hour
- Compact, economical plant with easy maintenance and spare part replacement
- Fully automated process, operated by only one person per shift
- Process that removes both organics and carbon from feedstock in a single step
- Removes heavy metals (e.g. zinc, lead) from the remaining metal stream at low temperatures
- Performance at emissions lower than European emission standards
- Independence from power suppliers due to own power generation from heat recovery
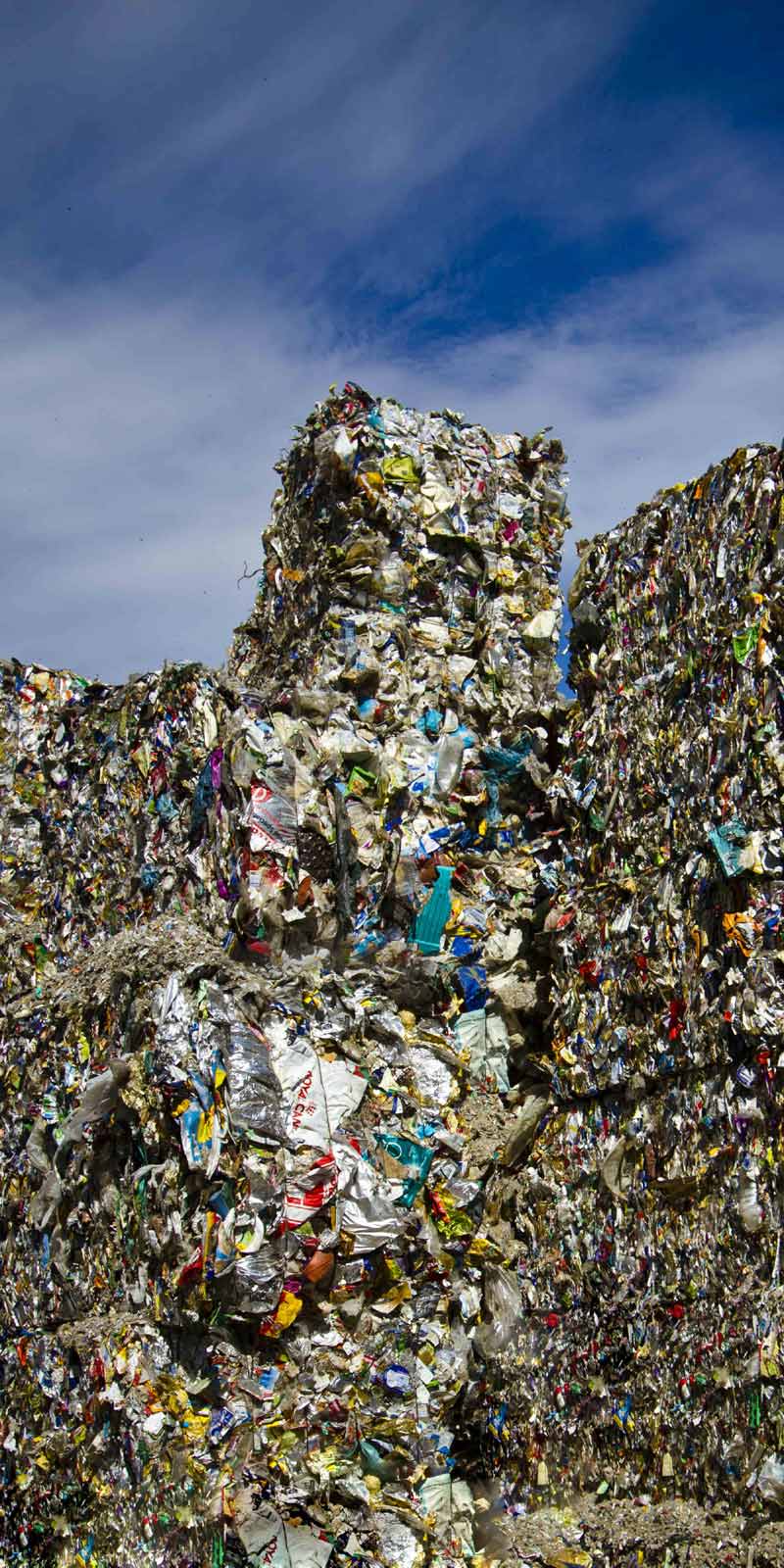
How does Pyradec® work?
The Pyradec® system is based on the fluidised bed principle. We believe that the application of this technology for the continuous cleaning of metals is revolutionary for the waste industry.
A fluidised bed is created when the amount of a stable, particulate substance behaves like a liquid due to the supply of compressed air. The material to be cleaned is transported through the “bath” of this substance. Unlike the pyrolysis process, which operates under oxygen-free conditions and in which the material is heated indirectly with flue gas, the Pyradec® cleans the material directly. A thermal reaction takes place when the material comes into contact with the 500 °C hot “liquid substance”.
Possible waste types:
- Consumer packaging with varying degrees of organic contamination.
- Aluminium beverage cans
- Mechanically sorted municipal waste
- Aluminium foil/beverage cartons
Industrial waste containing aluminium or other metals:
- Iso-Profiles
- Copper-bitumen mixture
- Window frames
- Cables
Special waste:
- Highly explosive wastes such as ammunition
- Highly flammable wastes such as filled aerosol cans
- Special wastes, e.g. medical wastes
Who is Pyradec® for?
Pyradec® provides a valuable tool not only for the metalworking industry, but also for municipal and commercial waste recycling.
Potential customers include:
- Secondary smelting
- Metal traders
- Communities / municipalities / cities
- Companies involved in waste collection and processing (disposal companies)
Smelting
While Pyralu® is the main product of PreZero Pyral, we are able to offer our customers aluminium in all forms, including ingots, dubs, pyramids, sows and liquid aluminium. This is made possible by our two smelters (with 2-chamber hearth furnace, salt drum furnace, and holding and casting furnace) including the necessary equipment.
Aluminium smelting plant
An important part of the integrated plant in Freiberg is the aluminium smelter.
Worldwide, the production of primary aluminium from bauxite requires a specific primary energy consumption of approx. 163,730 MJ/t aluminium. In contrast, secondary production of aluminium requires only 19,505 MJ/t aluminium and thus only 11.9% of the energy of primary production. Therefore, this metal is ideally suited for value recovery from urban mining (waste as a raw material source).
The aluminium obtained from pyrolysis is melted in a 2-chamber hearth furnace. In addition to this recycled aluminium, other aluminium scrap with low residual contamination is used in the smelting plant.
The heating chamber has recuperative air preheating and low NOx burners.
The aluminium is tapped and transferred discontinuously to a furnace for alloying, casting and holding.
The rotary salt furnace is mainly used for thin-walled and fine-grained aluminium scrap This means less power consumption at high output, which is in line with our efficient and resource-saving concept.
Part of the plant is a Gautschi casting belt with a fully automatic robot system for stacking and packing the ingots.